Announcing Our Investment in iCOMAT
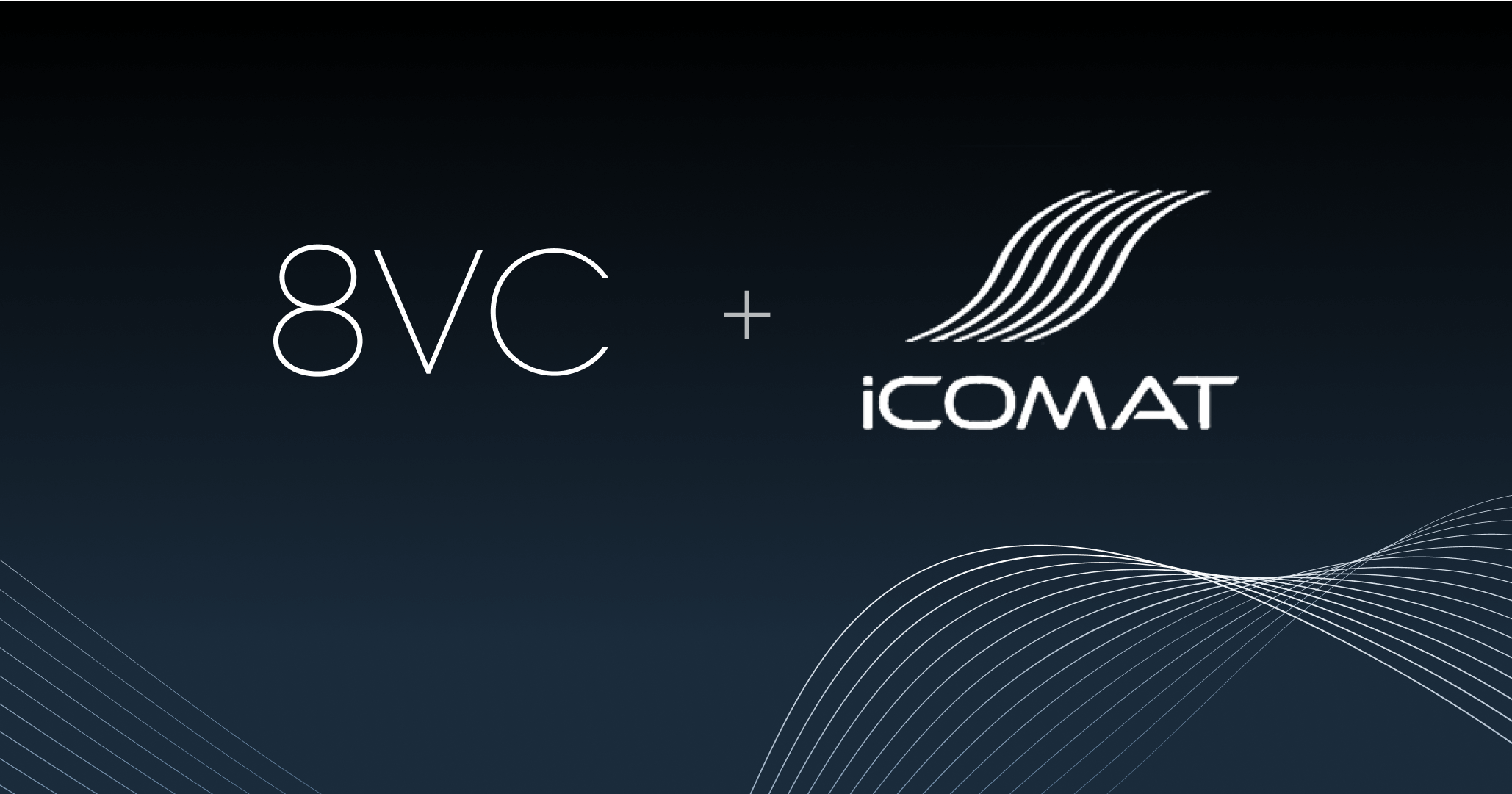
Share
While most discussion of aviation breakthroughs focuses on areas like VTOL, advanced fuels, electrification, or autonomy, weight is a universal concern. In commercial aircraft, lowering costs through methods including weight reduction has helped expand access to air travel from an estimated 383 million global air passengers in 1970 to almost 4.5 billion in 2019. In defense, weight reduction means greater range - increasingly critical with conflict looming in the Indo-Pacific. In recent decades, weight reduction has largely involved replacing metals with composites - most notably in Airbus’ A350 and Boeing’s 787 Dreamliner, with total reduction estimated at 20%.
Among composites, carbon fiber is the gold standard - as strong as steel at a fifth the weight. However, in addition to being expensive and time-consuming to produce, carbon fiber is also anisotropic: only strong in the direction of the fibers. This can be mitigated by layering fibers in different directions, but because structures are never loaded equally in all directions, doing so introduces excess material and costs. Ideally, carbon fiber would be aligned along the areas of greatest material stress, but unlike metals, traditional composites, made from layers of straight fibers, can’t bend without creating severe defects. To see why, imagine bending a ribbon.
iCOMAT (Innovation in Composite Manufacturing Automation Technology) has developed a breakthrough system that unlocks the advantages of carbon fiber composites for aircraft, space, and automotive components at a scale, production rates, and unit economics that drastically improve on legacy processes. Founded in 2019 by Dr. Evangelos Zympeloudis, iCOMAT builds on a decade of research at the University of Bristol, a global leader in composites. There is extensive research, dating from the 80s, focused on fiber steering, but the bottleneck has always been manufacturing - until now.
iCOMAT’s proprietary Rapid Tape Shearing (RTS) is the world’s first - and only - process capable of fiber steering without introducing defects, allowing carbon fiber to finally fulfill its industrial potential. Alongside RTS, iCOMAT has developed design and manufacturing optimization workflows for fiber steering, creating a digital thread linking design and manufacturing. By defining the fiber orientation at any point of a composite layer, iCOMAT massively expands the design space, resulting in lower weight, superior structural efficiency, and better performance.
.png)
.png)
Steering is also key to drastically improving production rates. Because composite materials are notoriously difficult to stamp or form, iCOMAT uses software to predict where defects/wrinkling will occur, pre-steering carbon fiber tapes in 2D so they can be formed in 3D. This enables a fully automated workflow, much like a stamping line at an automotive factory. The result is a full order of magnitude faster production compared to the previous state of the art, automated fiber placement (AFP).
iCOMAT’s structural and production benefits have been extensively validated in the most demanding applications. Compared to AFP (itself a small fraction of legacy carbon fiber production, which remains mostly manual), the advantages are dramatic:
1) Defense Aircraft Fuselage Panel: 4X faster production, 15% lighter, 30% cheaper.
2) Aircraft Curved Fuselage Frame: 17% lighter than straight fiber, defect-free, layup in 5.2 minutes per part vs 8.5 hours.
3) Civil Aircraft Lower Wing Skin Panel: 65% lighter, 3X faster production.
While iCOMAT is poised to be a major disruptor, they are also an enabler, with a proven ability to partner with industry giants. The company counts over 25 customers, including major US and UK defense primes, passenger vehicle OEMs, and Formula 1 teams. To satisfy current demand, iCOMAT has secured a $6 million match-funded grant from the UK Space Agency to stand up its first factory, a state-of-the-art 45,000 square foot facility in Gloucester, UK. This facility can handle R&D, as well as end-to-end production of composite parts up to 6 m x 2.5 m, from raw material to finished components, primarily for aerospace. Eventually, the capabilities unleashed by fiber steering will enable iCOMAT to create the first lights-out composites factories.
Today, we are pleased to announce iCOMAT’s $22.5 million Series A, co-led by 8VC and the NATO Innovation Fund. However, numbers tell only a fraction of the story, and a few reflections on why we invested are in order.
As with many of the problem spaces in our portfolio, aerospace and automotive are trillion-dollar industries still dominated by legacy processes, with the added burden of legacy materials. iCOMAT is revolutionizing both, using software-defined techniques to redraw physical boundaries and produce structures of previously unattainable intricacy and fitness for real-world rigors.
Crucially, the iCOMAT team supplies the scientific and industry leadership needed to take the torch from earlier composites pioneers. CEO and founder Dr Evangelos Zympeloudis developed iCOMAT’s core technology as a continuation of his Ph.D work, holds numerous key patents, and has consistently industrialized R&D breakthroughs. Interim MD Keith Fairbrass, formerly MD of Aerotron Composites and Director of Operations & Engineering at Cobham Composites, is a leading expert on composites manufacturing and production. Chairman Ben Olivier is the former CEO of Thales Alenia Space, UK, with a career spanning over four decades in the space industry. Head of Design Dr. Olivia Stodieck is the world’s leading authority on fiber steering for aeroelastic tailoring of aerodynamic structures. HR Director Rony Seamons is a veteran in scaling up technology companies.
Before the 1870s, steel was also a niche material, largely limited to hand tools - until Bessemer and Carnegie enabled mass production, giving rise to skyscrapers, railroads, heavy machinery, and other hallmarks of the Second Industrial Revolution. A quarter of a millennium later, iCOMAT is chasing a similar inflection point. We are honored to support their ambitions.